Passive Robot Kinematics
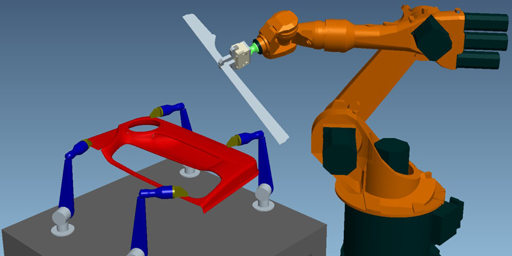
Hyper-Flexible Robot Cells Using Reconfigurable Passive Kinematics ECHORD-HYROPA
Manufacturing in small and medium-sized enterprises is characterized by a high diversity of variants and a frequent reconfiguration of tools and equipment. Here, the use of flexible industrial robots can only be achieved through the use of easy and intuitive robot programming technologies, as well as tools and grippers that can be reconfigured quickly.
In the HYROPA project the use of automatically reconfigurable passive articulated arms was examined, in order to enable the support of different work tasks in standard industrial robot cells. The newly developed passive kinematics are used in combination with various grippers to hold and manipulate work pieces with diverse geometries and dimensions in the workspace of an industrial robot. This expands the level of flexibility of existing robot cells and enables an easy adaptation to different work pieces.
The passive kinematics for this purpose can be locked in almost any position by clamping the individual joints. Reconfiguration of the passive kinematics will be done by the industrial robot: It temporarily releases the joints' clamping and newly positions the kinematic's arms. Thus, an automated change-over to almost any work piece is possible without manual intervention.
The flexibility of robot cells, especially in small and medium-sized enterprises, can be improved without substantially raising the robot cell's degree of complexity. The major advantages of using reconfigurable passive kinematics are the lower complexity and lower costs in the construction and operation of robot cells, while at the same time offering good adaptability to small production volumes.