Automated Inspection of Rotor Blades
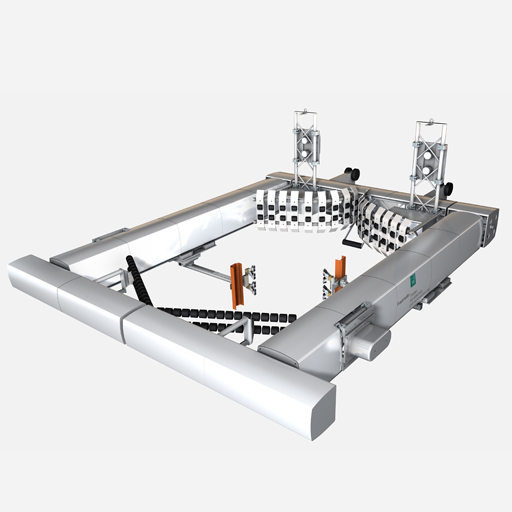
Robot for the Inspection of Wind Turbine Rotor Blades (RIWEA)
The objective of the RIWEA project was to develop novel technologies to completely capture the condition of wind turbine rotor blades. Such state-of-the-art inspection methods as thermography, ultrasonics and high resolution cameras in conjunction with innovative robots make a reliable, objective and integrated analysis of blade condition possible. Wind turbine rotor blades must be inspected for damage at regular intervals. Primarily made of glass fiber reinforced plastics, rotor blades are one of a wind turbine’s most highly stressed components.
The robot system consists of a frame structure that fully encloses the rotor blade and move on ropes along the rotor blade. This enables the robot to inspect every significant area of the rotor blade and autonomously adjust to its variable cross section. The frame structure can be opened mechanically so that the robot can automatically attach at the rotor blade, thus making the system compatible with any type of wind energy converter.