Inspection and Cleaning Robots for Sewer Systems: Damage Detection System
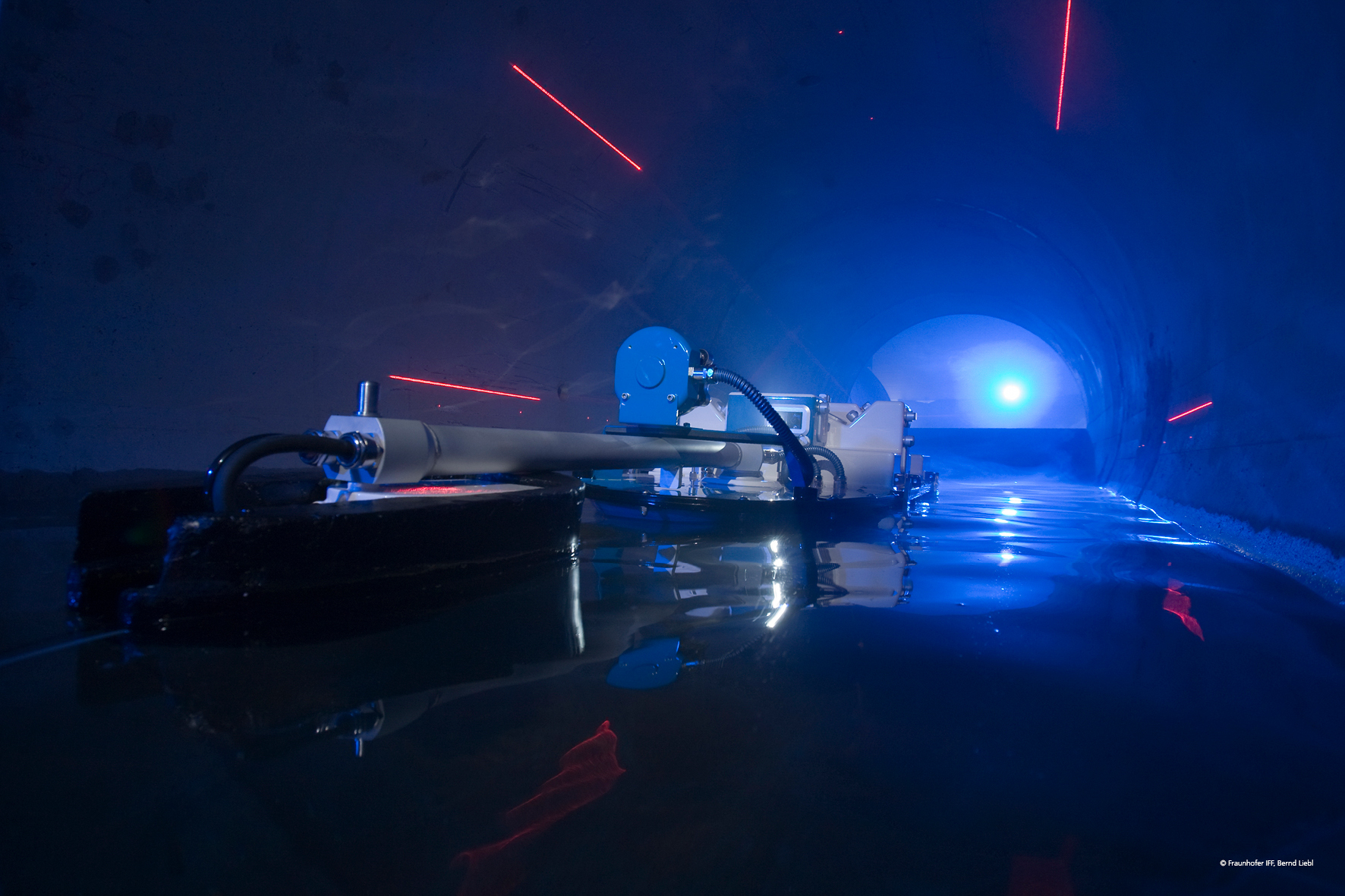
The inspection of large, partially filled, continually operating sewer lines constitutes a particular challenge for sewer operators. The damage detection system (SEK) developed by the Fraunhofer IFF for the Emschergenossenschaft is the first system in the world able to detect damage with high accuracy even in partially filled sewer lines.
To reliably perform inspections and monitor condition and enable operators to fulfill their legal obligations, the damage detection system is equipped with the following sensor systems
- a multi-camera system that detects cracks, corrosion and leaks above the water line and joint width
- an ultrasonic scanner that detects mechanical wear, deposits and obstacles below the water line
- video cameras that detect infiltration above the water line